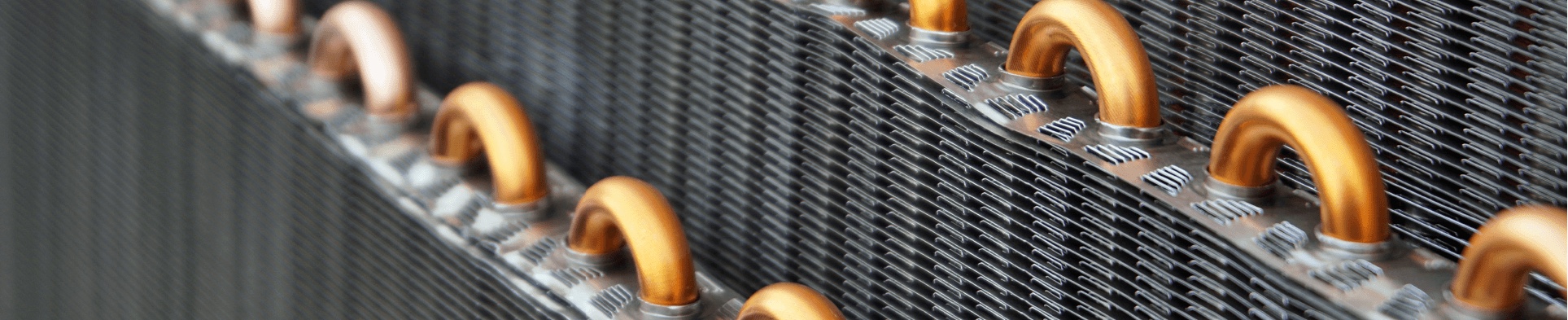
.Intelligent energy recovery
Air conditioning technology requirements are as complex as the concepts of technical construction. Modern air conditioning systems must use resources sustainably and be energy efficient. They should aim at minimising long-term energy consumption with no sacrifice of comfort. Laws, rules and regulations are all-important.
The classic but relatively inefficient closed loop system has been developed further with an optimised selection of components for high-efficiency energy recovery and low loss of pressure on the air side.
The innovative system employs highly efficient energy recovery technology in the ring network for spatially separated air supply and exhaust systems.
In a closed loop circuit, a pump is used to circulate an intermediate fluid between two or more high efficiency coil heat exchangers. The heat transferred to one coil by the warm air flow is transported by the intermediate fluid to the other coil, where it is transferred to the colder air flow. This system makes it possible to recover heat from several sources spaced apart from each other, and the air intake and exhaust locations can also be separated. Complete physical separation of the two flows and the consequent elimination of any risk of contamination make these systems suitable for use where very high hygiene levels are required, for example in hospitals, operating theatres, clean rooms, laboratories and food preparation sites, and in industrial air technology used for recovering energy from process heat, or heat from exhaust gases.
Our Flowbox hydraulic system transfers energy from one air flow to another. In addition, multifunctional heating or cooling energy can be fed into the flowbox. The choice of energy sources is almost limitless. Renewable energy resources in particular significantly improve efficiency. In order to maximise efficiency, we not only use highly optimised components, we also have a control system for the intelligent network and for control of all the individual components. Our control system optimises efficiency and reduces costs over time.
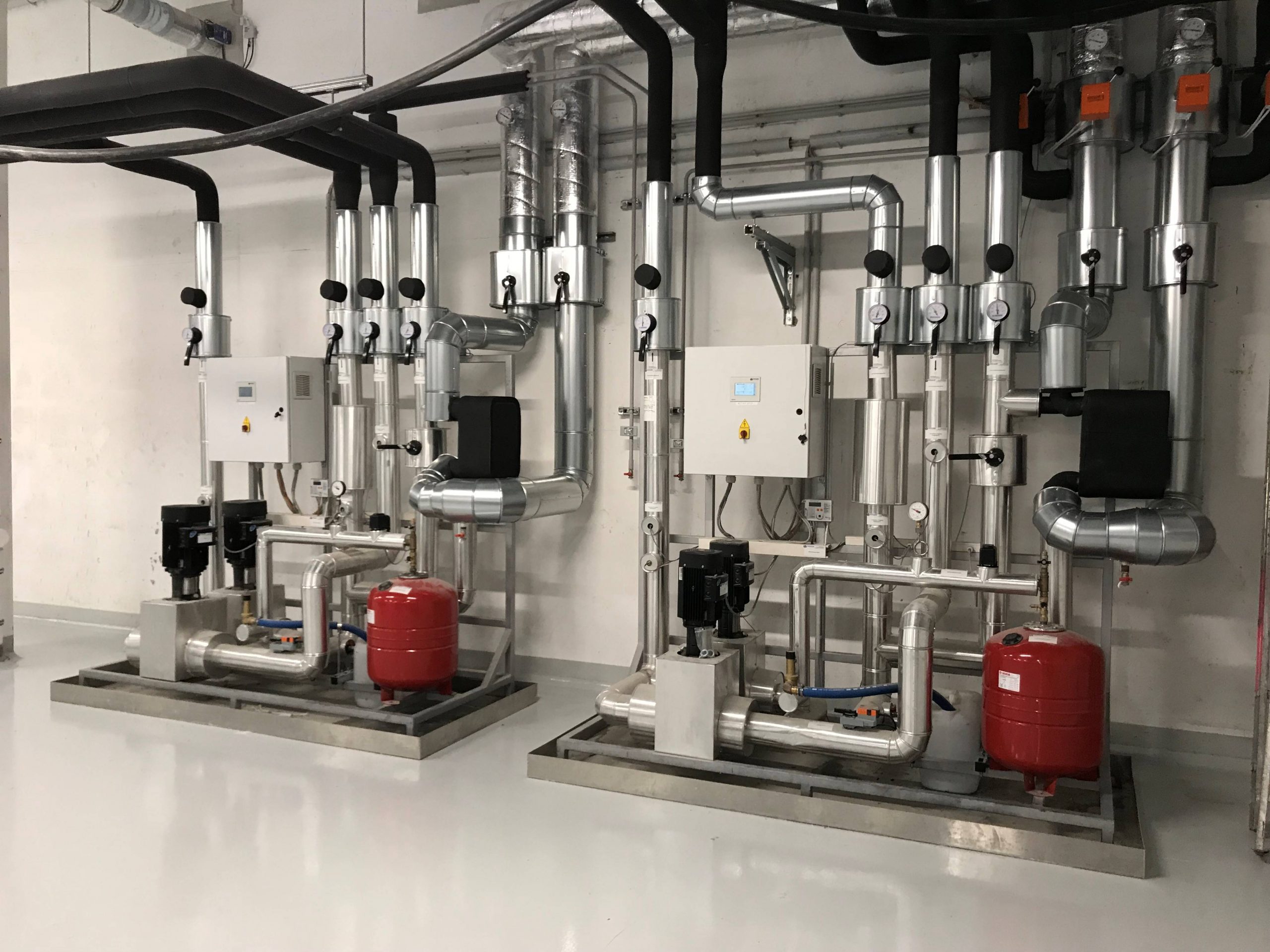
Energy in movement
Our hydraulic module is designed to ensure high energy saving efficiency. Selection of all components is based on energy criteria:
- Speed-controlled pumps with frequency converter and optional redundancy pump;
- Heat exchangers for additional heat and cold coming from various energy sources;
- Adiabatic air cooling (in the exhaust air flow)
- Heat pump;
- All required fittings, including: stop valves, check valves, over-pressure safety valves, pressure monitoring, automatic feed, flow monitor, dirt filters, heat meter, pressure gauge, thermometer, ice protection;
- Fully galvanised, stainless steel or copper piping, optionally insulated with sheet metal cladding;
- Control cabinet with mounted and wired control;
- Base frame housing all components;
- Soundproofed structure (optional)
- Weatherproof construction (optional)
All components are sized and installed according to need and requirements.
Closed circuit system
Flexible heat transfer
Our three available round tube geometries enable us to meet the performance, energy efficiency, size and hygiene requirements of a very wide range of applications.
Maximum flexibility: optimal geometry for every application. We are particularly skilled in developing heat exchangers of correct size and performance for recovery.
Our heat exchangers typically consist of copper tubes linked with strong aluminium collars for mechanical expansion. For critical applications, we develop various coating systems and use corrosion resistant materials (including stainless steel).
Our heat exchangers have a hundred percent counter-current circuit for greater efficiency. Despite the unconventional design, this circuit is completely vented by means of elbow vents and collection manifolds.
